camau-Magnetic levitation polishing machine is a kind of equipment that uses magnetic abrasive to polish the workpiece, which is applicable to the surface polishing treatment of various metal and non-metal parts. For aluminum die casting parts, the use of magnetic levitation polishing machine can achieve the following effects:
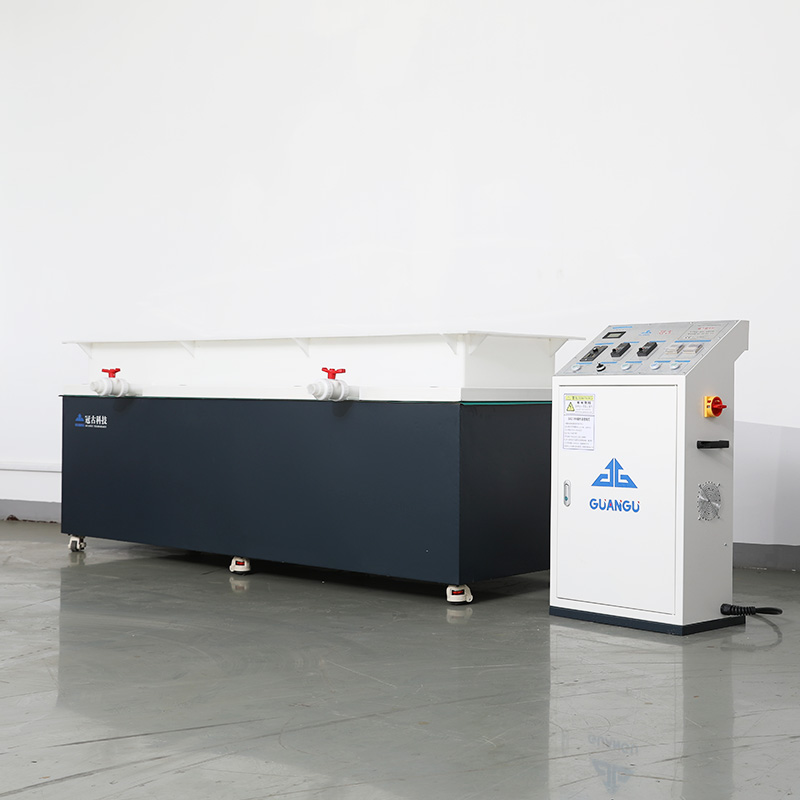
1.Improve surface finish: magnetic levitation polishing machine can remove casting defects, oxide skin, scratches and other microscopic unevenness on the surface of aluminum die casting parts, so that the surface finish reaches a higher standard.
2.Improve appearance: Through polishing, it can make the surface of aluminum die-casting parts smoother, reduce the uneven color and other appearance problems produced by the casting process, and enhance the aesthetics of the product.
3.Remove stress: the polishing process can remove the metal stress on the surface, which helps to reduce the deformation of the parts in the process of use.
4.Improve precision: Polishing can precisely remove tiny excesses on aluminum parts to ensure dimensional accuracy and shape precision.
5.Enhance corrosion resistance: the surface of aluminum die casting parts after polishing is smoother and less likely to accumulate dirt and corrosive media, thus improving its corrosion resistance.
6.Enhance the value of the product: after surface treatment of aluminum die casting parts not only improve the quality of appearance, but also increase the service life and reliability, which helps to enhance the competitiveness of the product market.
7.Energy saving and emission reduction: magnetic levitation polishing machine adopts magnetic abrasive, compared with the traditional polishing method, it has higher material utilization rate, reduces the use of abrasive and the waste produced, which is conducive to environmental protection.
When using the magnetic levitation polishing machine for polishing treatment, you also need to pay attention to the selection of the appropriate abrasive, polishing fluid and control of the polishing process, such as pressure and speed parameters to ensure that the best polishing effect is achieved. At the same time, the operator should follow the safety operating procedures to ensure production safety and personnel health.